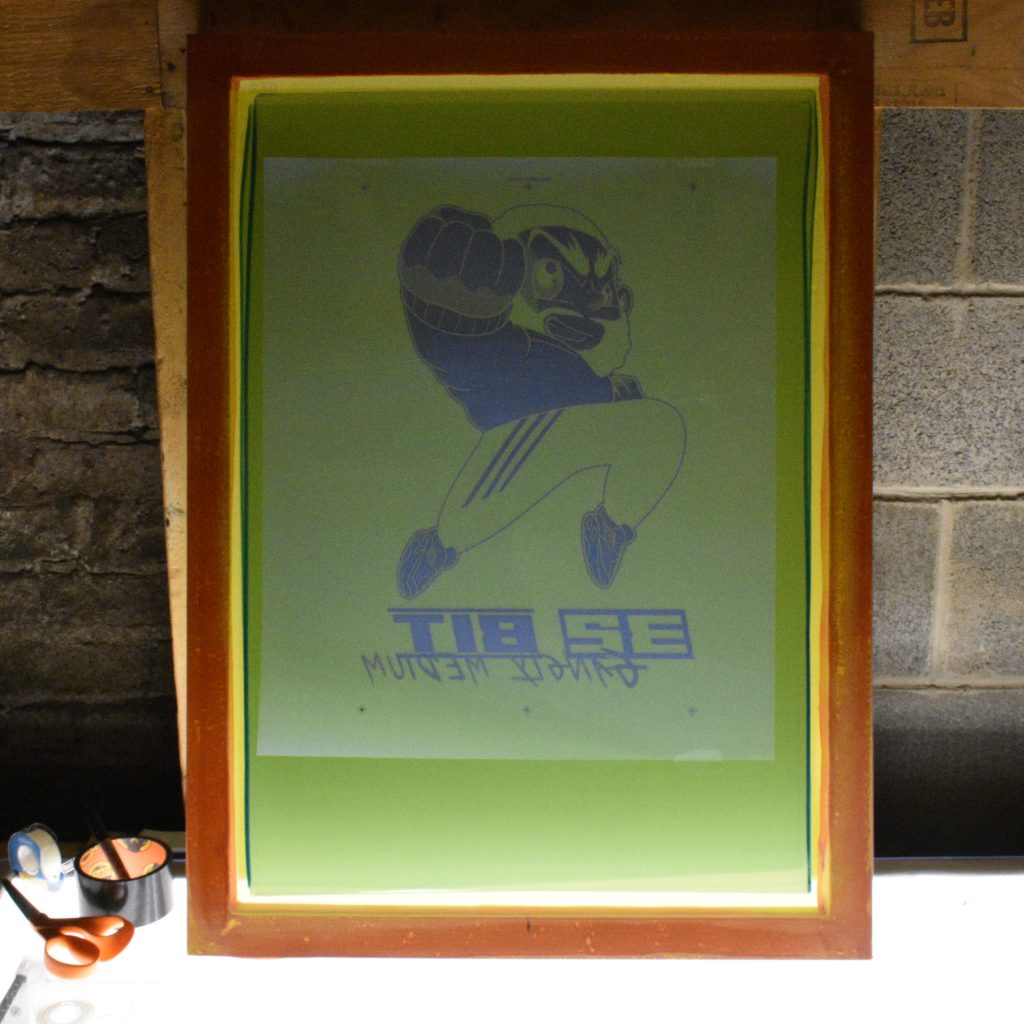
Screen-Printing : noun
the technique of creating a picture or pattern by forcing ink or metal on to a surface through a screen of fine material.
Method Printing is a prominent Chicago-based screen printing shop that takes pride in delivering top-quality results. With our diverse range of screen printing services, including plastisol, water-based, and discharge printing, we have the expertise to meet your specific printing needs. But you might be wondering, “What is screen printing, and is it the right choice for my next custom printed t-shirts?”
Screen printing, also referred to as silkscreen printing, is a highly versatile and time-tested method of applying intricate designs onto a wide array of fabrics and materials, with t-shirts being one of the most popular choices. The process involves creating a stencil, commonly known as a screen, which acts as a medium to transfer ink onto the chosen surface. Each color within the design requires a separate screen, and ink is meticulously applied to the fabric one color at a time, layer by layer.
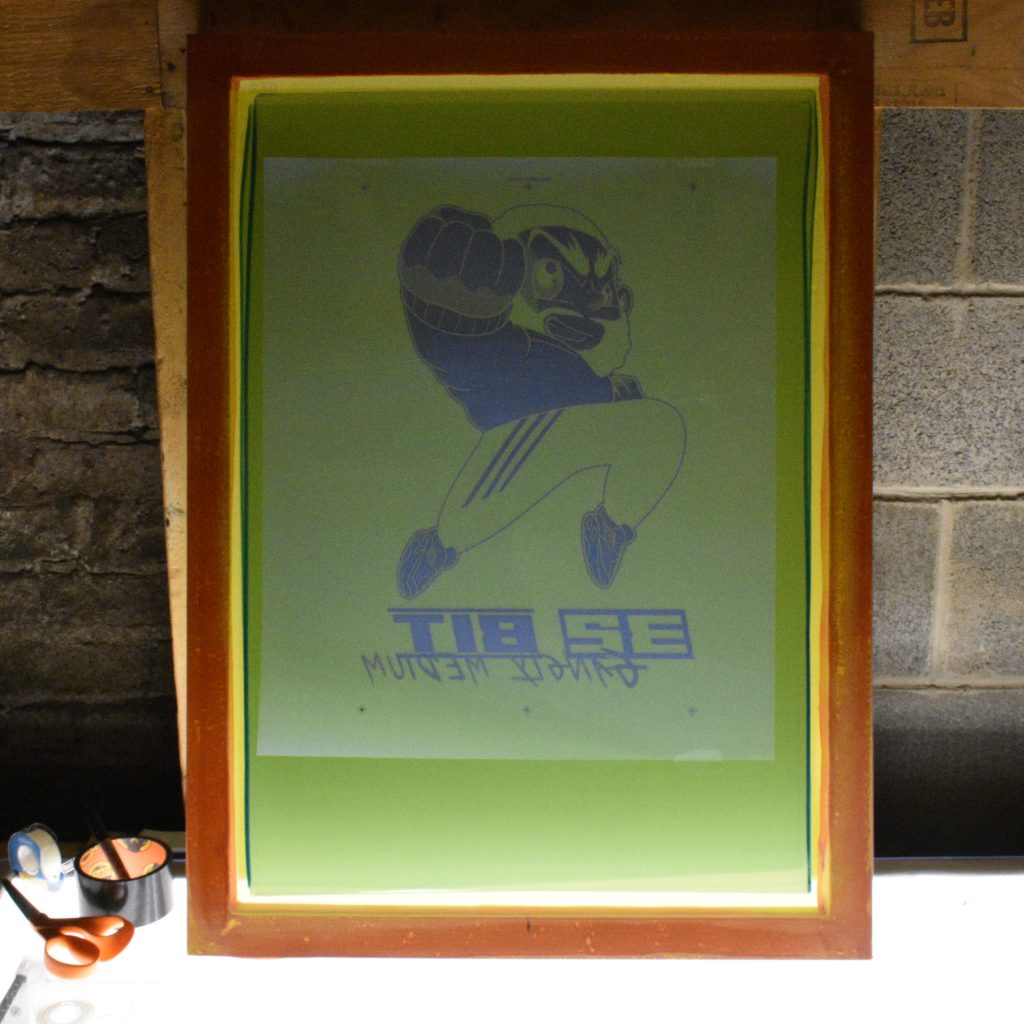
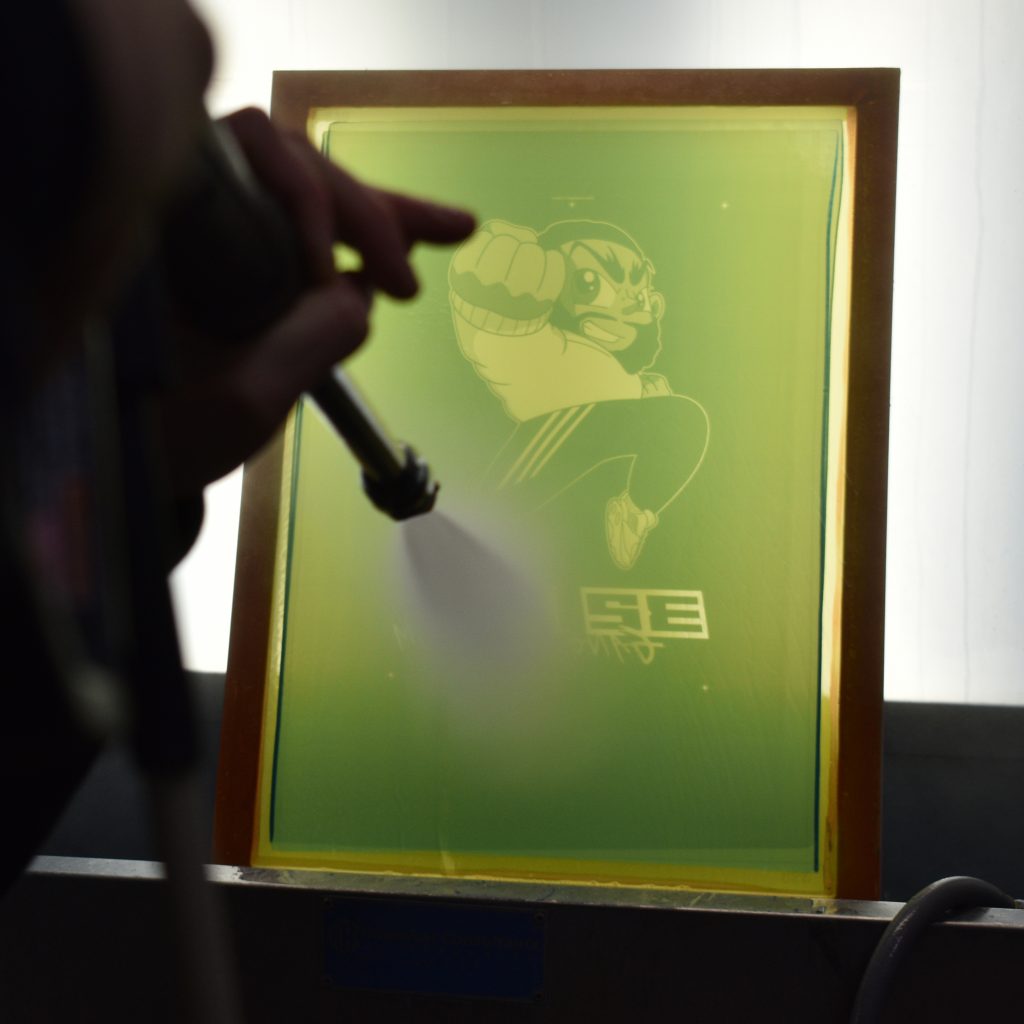
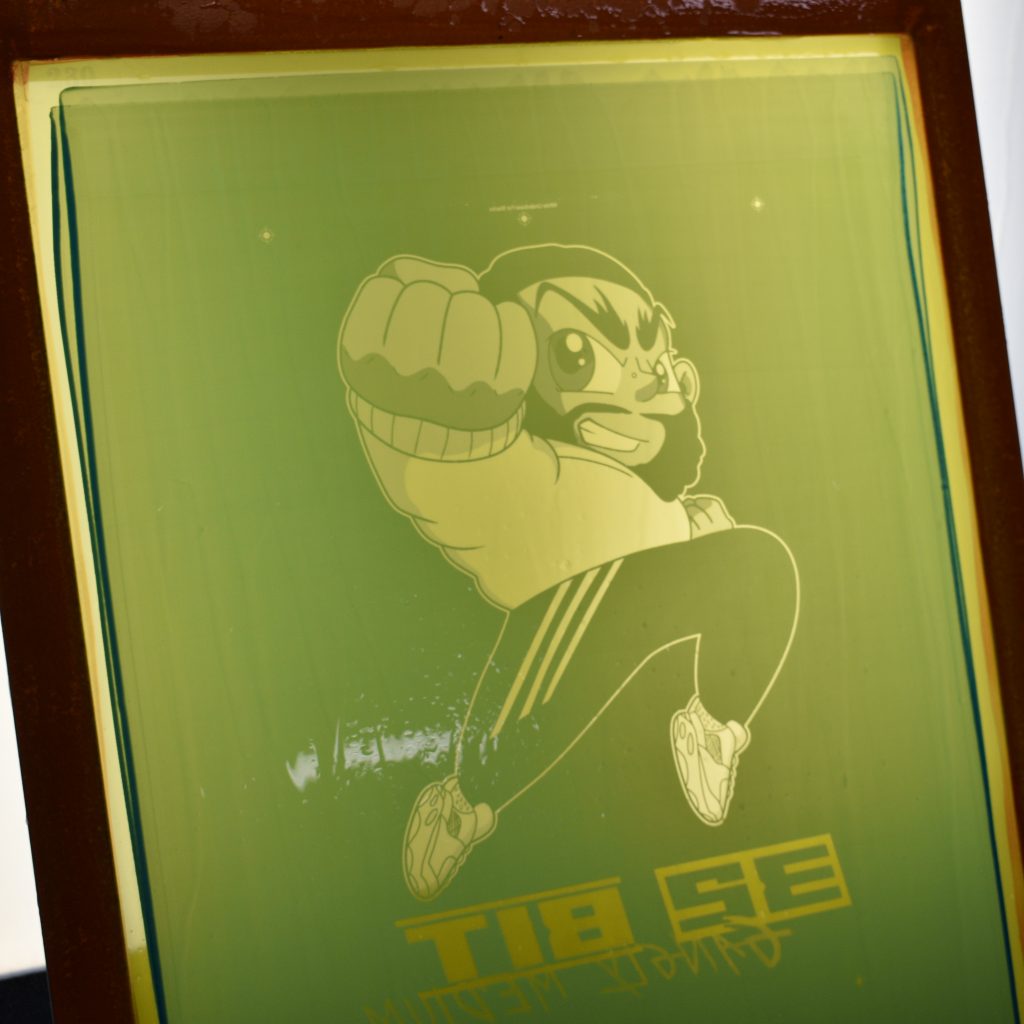
One of the key advantages of screen printing lies in its ability to produce vibrant and long-lasting designs. The ink used in screen printing is applied in a thicker layer compared to other printing techniques, ensuring that the colors remain bold and vivid, even after multiple washes. The method’s exceptional durability allows custom printed t-shirts to retain their striking appearance and high-quality finish, making them ideal for frequent use and everyday wear.
The precision of screen printing enables the creation of intricate and detailed designs that accurately replicate artwork and graphics. It is particularly suitable for designs with solid, bold shapes and a limited number of colors, ensuring each element appears crisp and defined. From simple logos and text to elaborate illustrations and photographs, screen printing can faithfully reproduce a wide range of designs, making it a preferred choice for various custom apparel and promotional items.
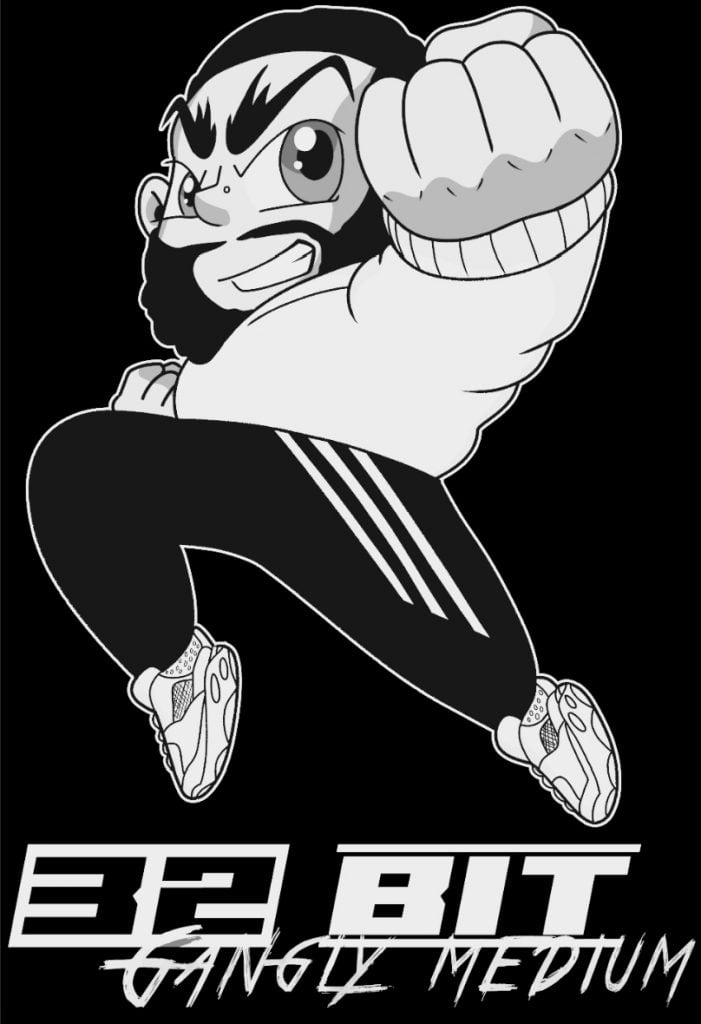
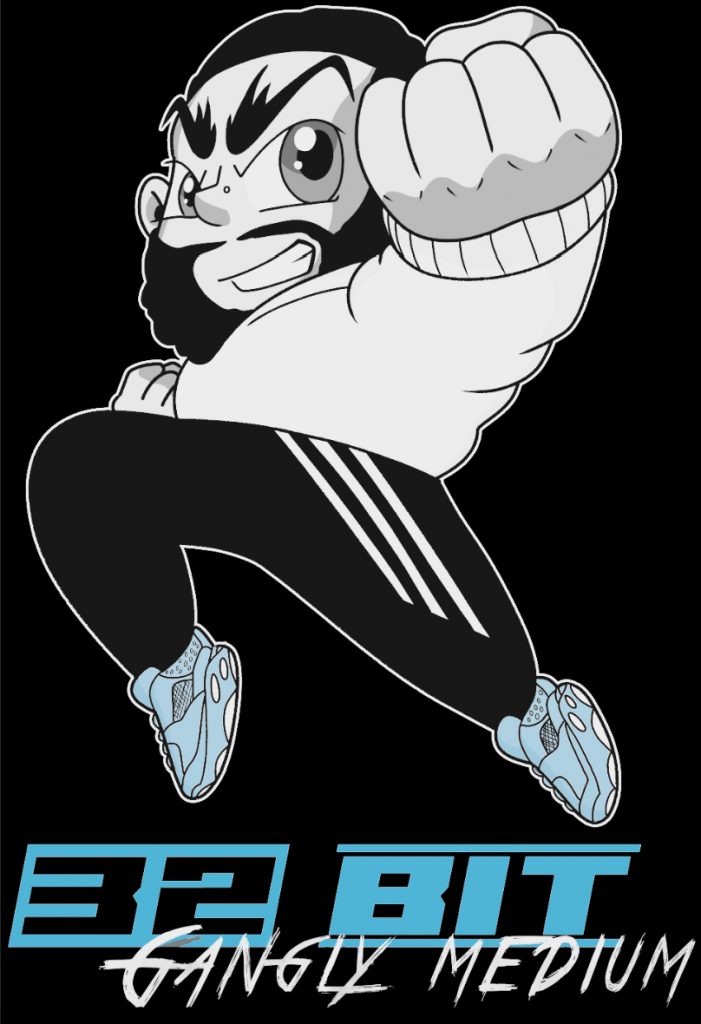
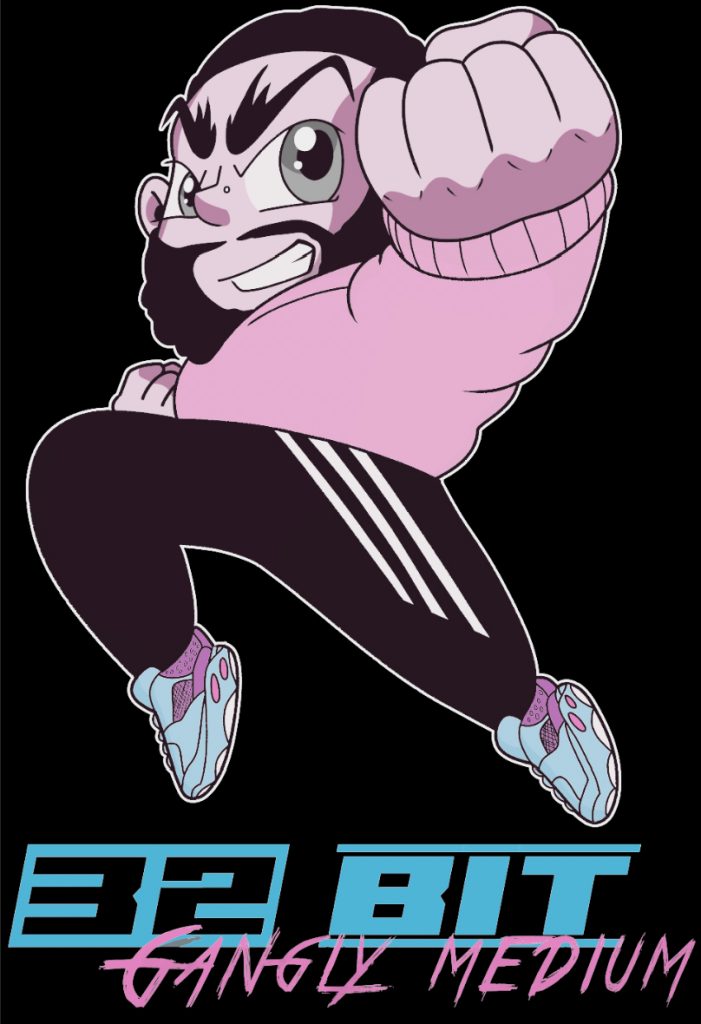
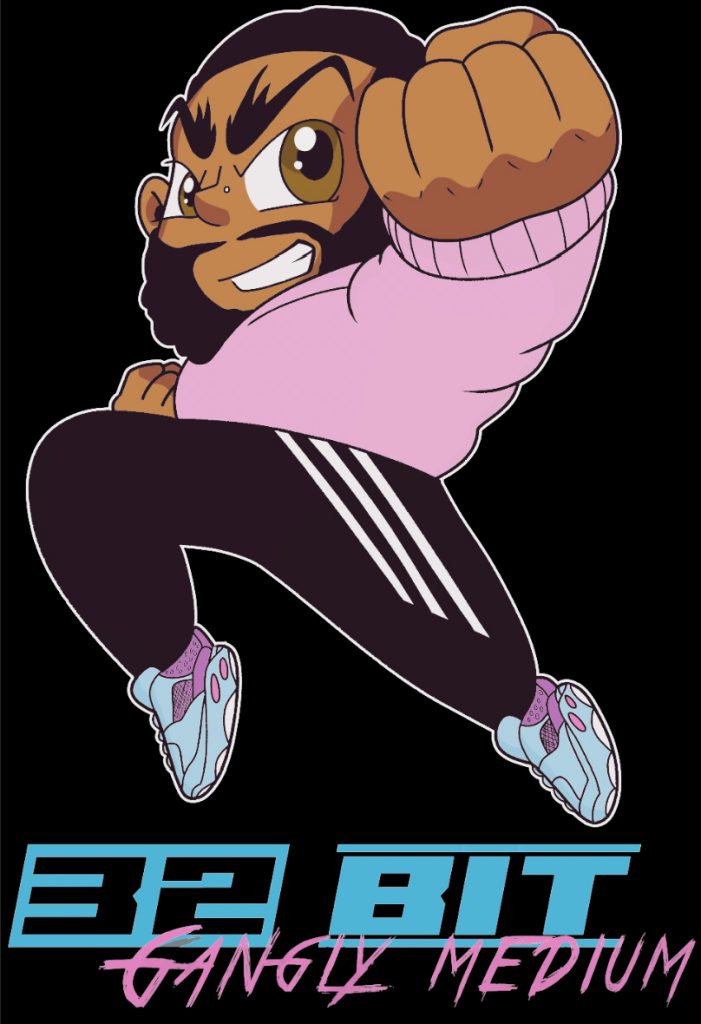
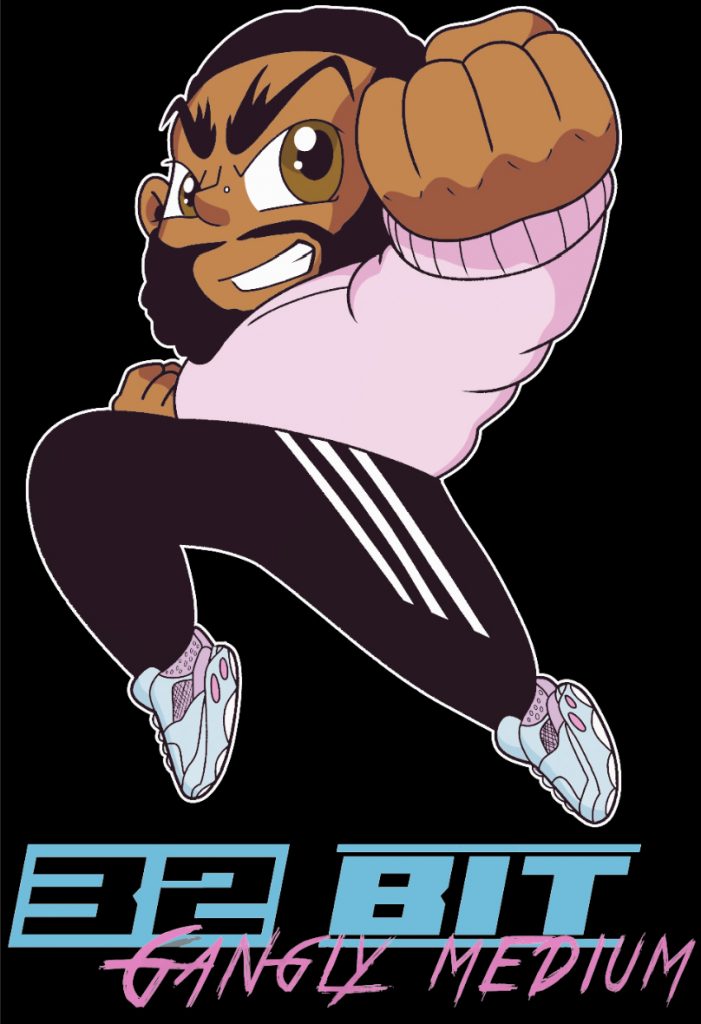
As a highly scalable technique, screen printing is well-suited for both small and large-scale production runs. Whether you need a limited batch of custom t-shirts for a small event or a bulk order for a larger campaign, screen printing offers cost-effective solutions without compromising on quality. This makes it a popular choice for businesses, sports teams, schools, event organizers, and individuals alike.
In summary, screen printing’s ability to transfer intricate designs onto fabrics like t-shirts, coupled with its vibrant and durable results, has solidified its position as a timeless and popular printing method. Its versatility, precision, and cost-effectiveness make it a favored choice for those seeking outstanding custom printed t-shirts that are sure to leave a lasting impression.

At Method Printing, our team of skilled professionals is dedicated to delivering outstanding results and exceeding your expectations. Whether you need t-shirts for a promotional event, team uniforms, or branded apparel for your business, screen printing can offer the versatility and durability you seek.
If you’re ready to take your custom t-shirts to the next level with screen printing, contact us today to discuss your project. Our friendly staff is more than happy to assist you with any questions and help you make an informed decision about the best printing method for your unique needs. Let us transform your ideas into stunning reality with our top-notch screen printing services.
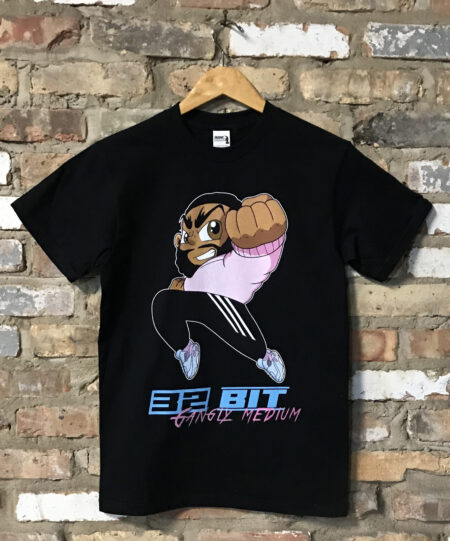
Why Go With Screen Printing VS Direct To Garment Printing?
When deciding between Screen Printing and Direct to Garment Printing (DTG), it’s essential to understand the advantages of each method to make the best choice for your custom apparel needs.
Screen printing stands out with its remarkable longevity and fewer limitations compared to DTG printing. The screen printing process allows for vibrant and durable designs that can withstand the test of time, making it ideal for long-lasting and frequently used garments like t-shirts. Moreover, screen printing offers exceptional versatility, accommodating a wide range of fabrics and materials beyond just garments, expanding its potential applications for various promotional items and personalized merchandise.
On the other hand, DTG printing is favored for its lower minimum order requirements, making it a cost-effective choice for smaller projects under 25 pieces. This digital printing method allows for printing with intricate details and an unlimited color palette, enabling you to bring even the most complex designs to life. However, it’s important to note that DTG printing is not as efficient or cost-effective for larger-scale projects due to the nature of the process and the time it takes to print each individual garment.
When it comes to costs, screen printing often becomes the more economical choice for larger orders. Once you meet the 25 piece minimum requirements set by Method, the per-piece cost of each shirt decreases significantly compared to opting for a DTG vendor. This makes screen printing an attractive option for businesses, organizations, and events looking to produce custom apparel in bulk.
Ultimately, the decision between screen printing and DTG printing depends on the specific needs and goals of your project. If you prioritize longevity, versatility, and cost-effectiveness for larger quantities, screen printing emerges as the optimal choice. However, if you require smaller quantities DTG printing may be the better fit.
At Method Printing, we specialize in screen printing, delivering top-quality custom apparel that not only looks outstanding but also stands the test of time. Our expert team is here to guide you through the process and help you make the best decision for your custom apparel project. Contact us today to learn more and explore the possibilities of screen printing for your unique needs.
If you would like to learn more about the screen printing process view this blog article :
Screen Printing Terms